以世界级行业高标准打造的广汽传祺宜昌智慧工厂2019年6月底竣工,实现生产自动化、信息数字化、管理智能化及节能环保。单线生产节拍可达52秒;冲压、焊接、喷涂最大程度地实现了“生产自动化”;底盘合装,风挡玻璃、座椅,均实现了100%自动化安装。涂装车间率先引入最新一代的E-CUBE干式分离系统,实现了喷漆生产过程中污水0产生、0排放,同时极大地减少了VOCs排放。
相隔一年多,来看ABB及发那科对这个项目的更深入介绍。
每46秒拼装一辆汽车
刷新ABB柔性白车身总拼线节拍新纪录的是:广汽传祺宜昌工厂46秒/辆的下线速度。相比ABB为世界其他汽车工厂提供的生产节拍约60秒或最快达到的51秒,宜昌工厂的46秒意味着效率提高了23%。
为实现46秒节拍目标,ABB GateFramer柔性总拼系统被改造,配置的机器人增加到18台(以往项目最多配置14台),可在10秒内完成车身部件定位,16秒内完成狭小车身空间至少72个焊点的焊接。支持最多6种车型混线生产,仍能保持46秒生产节拍。
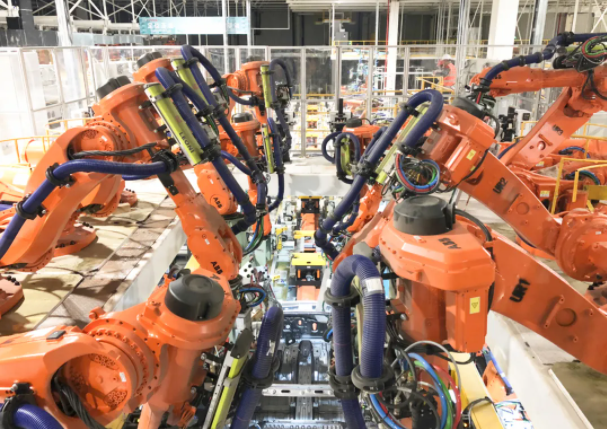
速度保障还需靠焊接车间主线的一条长达96米的ABB FlexTrack导轨进行车体传送,工位间仅需6秒到达,速度达到1500mm/s。
每42秒涂装一辆汽车
同样,作为机器人四大家族之一的发那科也在整车喷涂上给广汽传祺提供了更快更节能环保的方案,实现42秒完成一辆汽车的喷涂作业。整车涂装工厂采用B1B2水性油漆工艺,双线生产,共装备有56台FANUC喷涂机器人,车身喷涂双线86JPH(辆/小时)。此外,合成树脂工厂采用了水性涂料油漆工艺,并装备有14台FANUC机器人。
采用的喷涂机器人兼具开关门功能,配置的机器人数量因此减少16台。采用水性涂料直接加电技术使上漆率提升15%,杯+杯工艺应用则节约了大量材料成本。而上海发那科首次集成直接加电雾化器应用在保险杠水性喷涂工艺,效果较空气杯提升油漆利用率30%,降低生产成本。
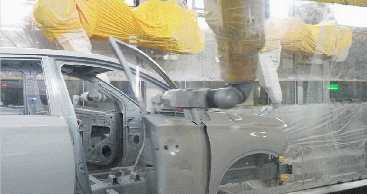
广汽斥巨资打造的宜昌智慧工厂,已体现两大世界级机器人企业的高强本领,ABB实现最快总拼线节拍,发那科提升上漆率降低生产成本。打天下还需自身本领硬,期待以后标杆工厂的打造出现更多国内机器人企业的身影。
来源:ABB机器人、发那科机器人、广汽传祺
智汇+平台整理发布